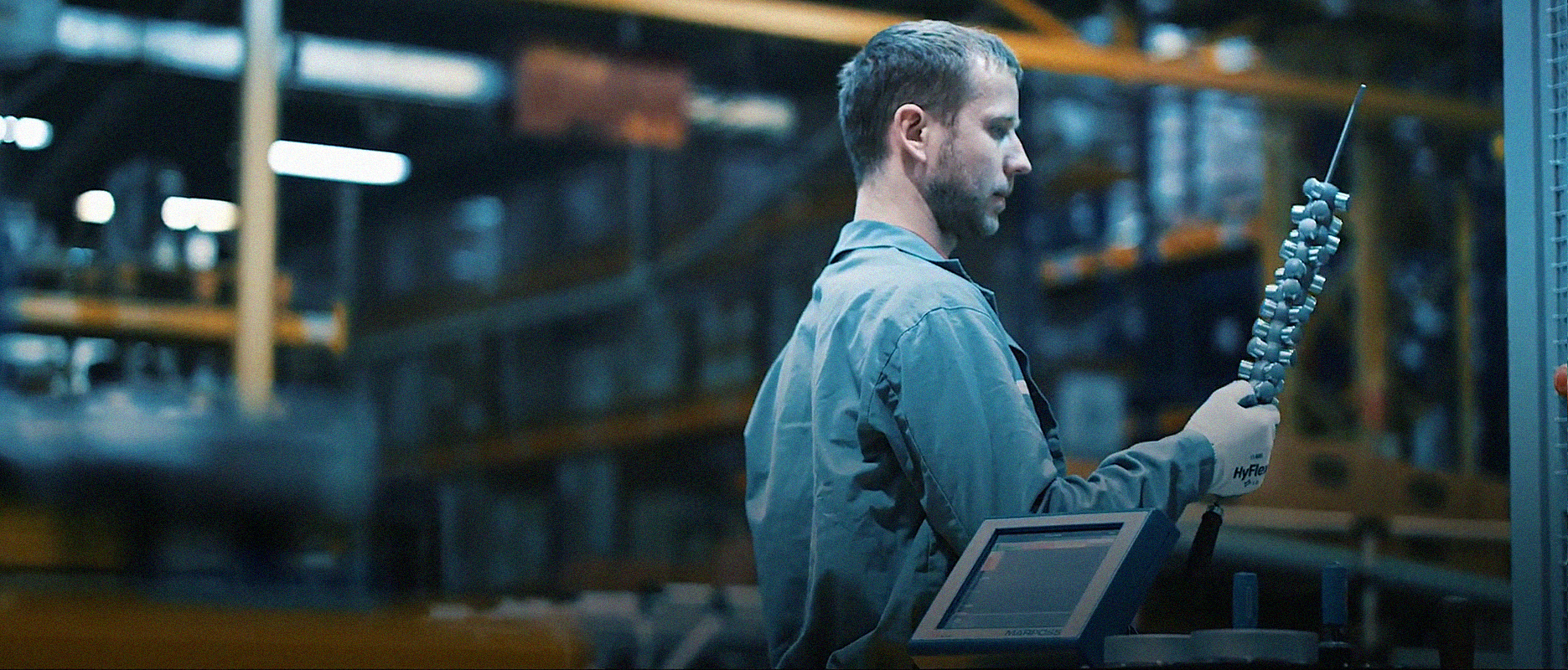
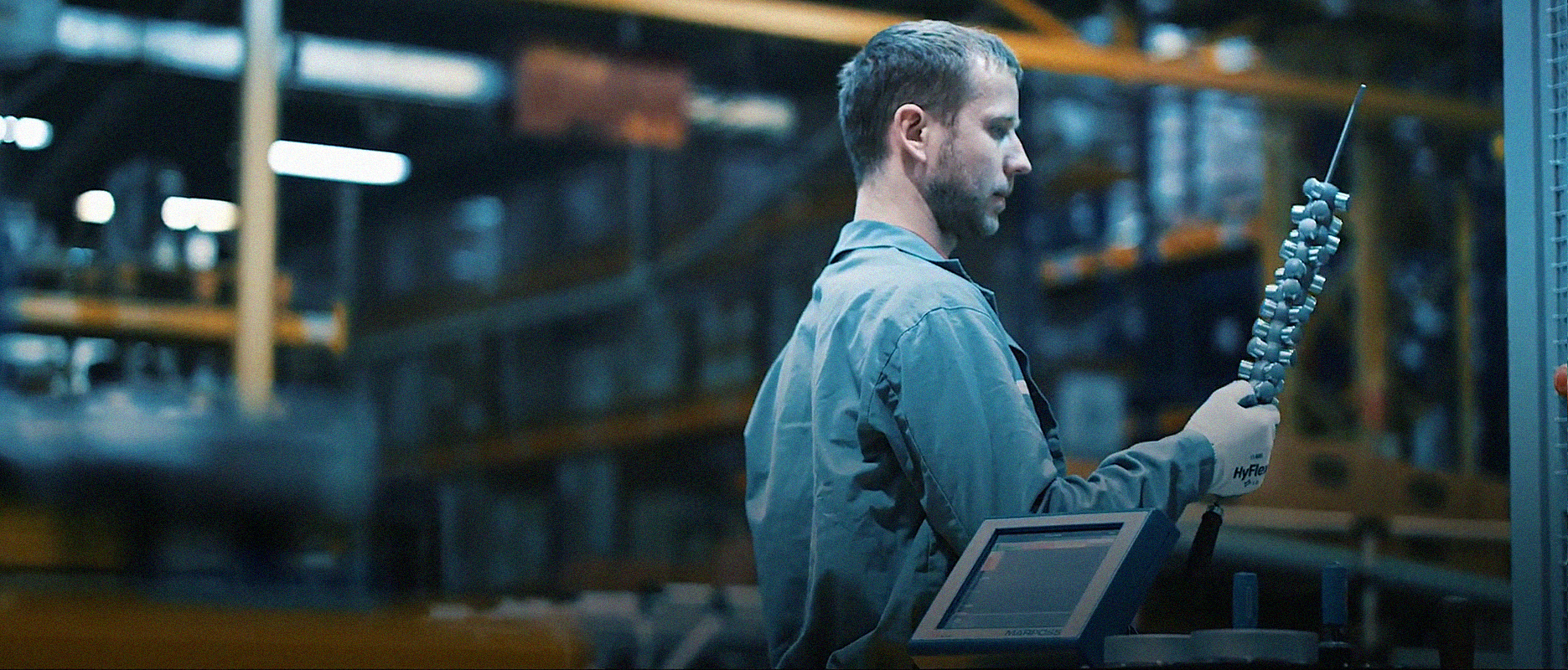

Manufacturing
Advanced Manufacturing Capabilities and Globally Sourced Materials Provide Superior, Cost-effective Products
Neapco operates modern manufacturing locations throughout North America and Europe. At all locations, products are manufactured using the most advanced computer-controlled machinery and globally sourced materials to provide superior products at competitive prices. Neapco production plants use lean manufacturing, synchronous material flow, and demand-oriented manufacturing principles to optimize customer value.
Automated High-volume Workflows and Process Improvements
Our Lean Enterprise at Neapco (LEAN) workflow incorporates the latest manufacturing innovations, including value-stream mapping (VSM), rapid continuous improvement (RCI), total productive maintenance (TPM) and Visual Factory.
Manufacturing capability highlights include:
- Flexible assembly cells — Assembly of aluminum and steel driveshafts in single piece or multi-piece configurations
- Advanced tube assembly construction — Grob forming of splines into steel and aluminum tubing
- Advanced welding techniques — Friction welding of steel and aluminum, double- and single-ended magnetic impelled arc (MAB), automated gas metal arc (Pulse MIG)
- Automatic assembly straighteners — Automated correction to straighten shafts where necessary and improve balance
- State-of-the-art Vision System — Fully automated quality assurance to detect proper assembly and verify all parts are in place eliminates 100% visual inspection while ensuring quality and safety
- In-house heat-treating and high speed dynamic balancers — Produces ideal tolerances and durability
- Precision CNC 4-axis transfer machining and CNC turning — Produces close tolerance repeatedly on products
- Goss-Porta high-speed CNC transfer machine with robotic gantry — Able to produce over two million yokes a year
A full range of automated manufacturing capabilities:
- Automated hollow milling
- Vertical and horizontal broaching
- Centerless and cylindrical grinding
- Automatic welding and driveline assembly
- Automatic precision tube cut-off
- Automated straightening of driveshaft tubing
- Digitally controlled driveline balancing
- Extrusion forming
- High-volume production using multi-spindle chuckers
- Internal diameter grinding
- Manual and automatic needle loading
- Specialized CV joint manufacturing
- Spline hobbing
- Spline and thread rolling
Neapco manufacturing plants are equipped with the latest advanced production machinery and
workflow processes to provide maximum defect-free throughput.